CNC Machining plays a pivotal role in delivering custom metal parts with unmatched precision, efficiency, and complexity. As industries such as automotive, machine building, and automation demand increasingly intricate components, CNC machining techniques have evolved into powerful enablers of innovation and quality.
This article deeply explores seven top CNC machining techniques essential for custom metal parts manufacturing, combining insights from industry best practices and reflecting on the expertise of CNCRUSH — a China-based factory with 12 years of experience providing high-quality cnc machining service focused on CNC Milled parts and CNC Turned parts.
Introduction
CNC Machining remains the backbone technology for producing complex custom metal parts with superior accuracy and surface finish. From rapid prototyping to mass production, CNC machining accommodates diverse material needs and design challenges.
With the steady growth in sectors like automotive, machine building, and automation, demand for precision-crafted components has skyrocketed. CNCRUSH has proudly served these industries for over 12 years, specializing in cnc machining service that delivers precision CNC Milled parts and CNC Turned parts meeting strict client specifications.
1. CNC Machining Technique 1 — High-Speed CNC Milling for Complex Geometry
High-speed CNC milling enhances machining efficiency and surface finish by using elevated spindle speeds and optimized feed rates. This technique reduces cycle times while maintaining tight tolerances and minimal thermal distortion.
CNCRUSH employs high-speed milling on advanced 4-axis and 5-axis machines, enabling intricate shapes required in automotive components such as engine brackets and precision housings in automation systems.
2. CNC Machining Technique 2 — Multi-Axis CNC Milling for Intricate Parts
Multi-axis CNC milling (4-axis and 5-axis) allows simultaneous movement of the cutting tool across several axes, enabling the manufacture of highly complex shapes with fewer setups.
This technique drastically reduces manual intervention, enhances dimensional accuracy, and facilitates the production of sophisticated CNC Milled parts essential for machine building equipment with tight geometric constraints.
3. CNC Machining Technique 3 — Precision CNC Turning for Cylindrical Components
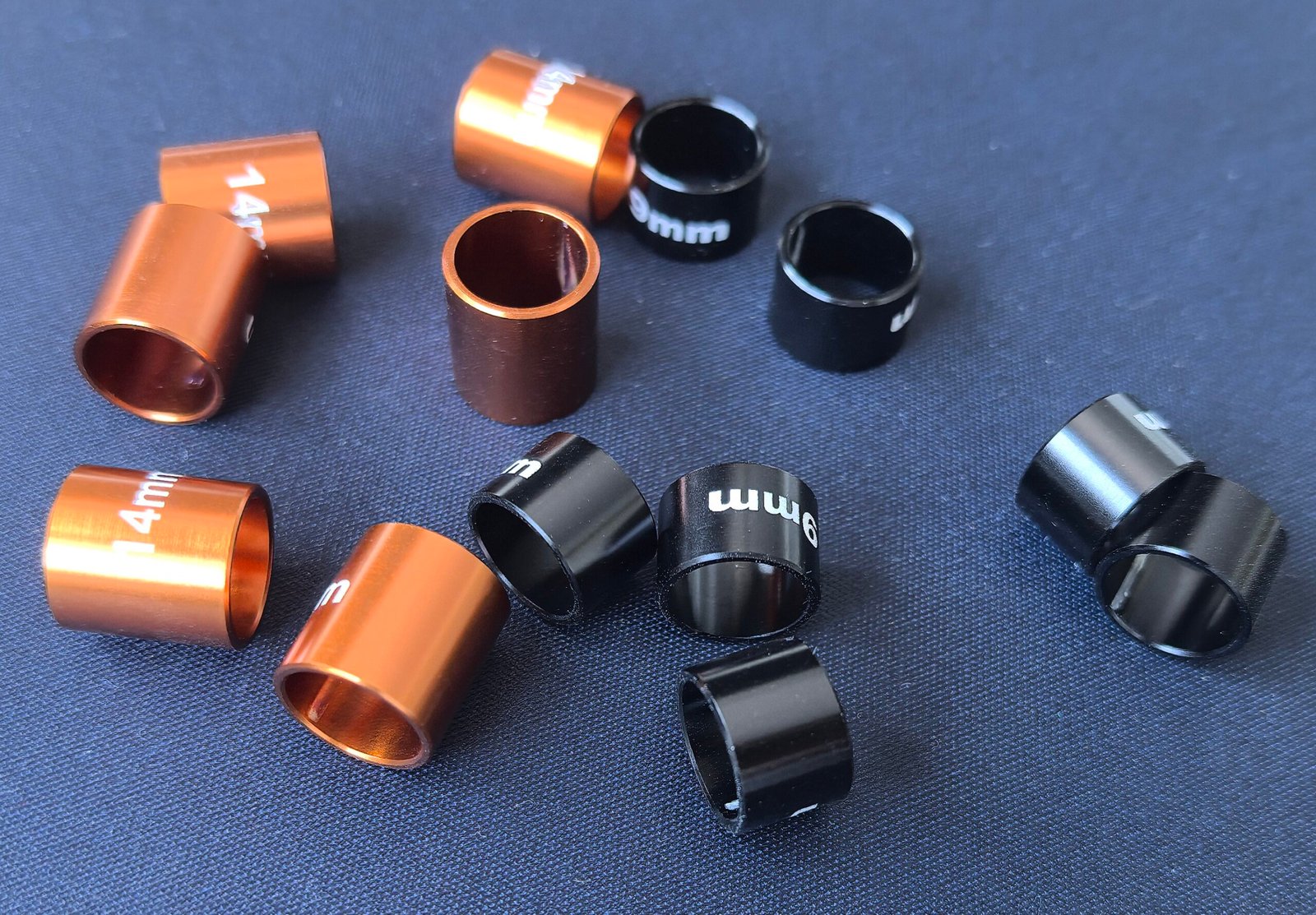
CNC turning is critical for creating symmetrical, rotational parts like shafts, pins, and collars with high precision and repeatability.
At CNCRUSH, we combine CNC turning with milling processes to produce custom metal parts that meet demanding dimensional and surface finish standards for the automotive and automation sectors.
4. CNC Machining Technique 4 — Advanced Surface Treatment for Enhanced Durability
Surface treatment techniques such as anodizing, polishing, and coating extend component life and improve corrosion resistance.
Through integrated CNC processes and surface finishing, CNCRUSH ensures that CNC Milled parts and CNC Turned parts not only meet mechanical specifications but also exceed longevity expectations, a crucial factor in harsh machine building environments.
5. CNC Machining Technique 5 — Optimized Toolpath Strategies to Maximize Efficiency
Effective toolpath programming reduces machining time and tool wear. Techniques such as adaptive clearing and trochoidal milling allow continuous cutting with reduced load.
Our skilled CAM programmers at CNCRUSH implement advanced toolpath strategies to enhance machining efficiency while maintaining the superior quality expected from our cnc machining service.
6. CNC Machining Technique 6 — Material-Specific Machining for Optimal Results
Different metals require customized machining parameters to balance tool life, surface finish, and dimensional stability.
CNCRUSH specializes in machining a wide range of metals including aluminum, stainless steel, and engineering plastics — tailoring the CNC process to meet the exact needs of CNC Milled parts and CNC Turned parts customers in the automotive, machine building, and automation industries.
7. CNC Machining Technique 7 — In-Process Inspection and Quality Control
Real-time monitoring and measurement during CNC machining drastically reduce scrap and rework.
Our factory integrates Coordinate Measuring Machines (CMM) and spindle probes for in-process inspection, ensuring every part conforms to tight tolerances — a commitment that defines our trusted cnc machining service.
Table 1: Comparison of CNC Machining Techniques for Custom Metal Parts
Technique | Key Advantage | Typical Applications | Impact on Quality |
---|---|---|---|
High-Speed Milling | Faster cycles, better surface finish | Complex automotive brackets | Reduced thermal distortion |
Multi-Axis Milling | Complex geometries with fewer setups | Aerospace and machine building parts | Enhanced dimensional accuracy |
CNC Turning | Symmetrical components with precision | Shafts and pins in automation | Superior roundness and finish |
Surface Treatment | Increased durability and corrosion resistance | Outdoor machine parts | Prolonged service life |
Optimized Toolpaths | Reduced tool wear and cycle time | High-volume production | Cost efficiency and consistency |
Material-Specific Machining | Tailored parameters per metal | Mixed metal product lines | Minimized defects and improved finish |
In-Process Inspection | Real-time quality assurance | High-precision sectors | Lower scrap rates, higher yield |
Table 2: CNCRUSH CNC Machining Service Overview
Service Aspect | Details |
---|---|
Years of Experience | 12+ years |
Core Capabilities | CNC Milling and Turning |
Materials Processed | Aluminum, Steel, Plastics |
Industries Served | Automotive, Machine Building, Automation |
Quality Control Equipment | CMM, Spindle Probes |
Production Volume Capability | Prototype to Mass Production |
Tolerance Achieved | ±0.005 mm or better |
FAQ Section
Q1: What makes CNC Machining essential for custom metal parts?
CNC Machining offers unparalleled precision, repeatability, and flexibility required to manufacture complex metal components tailored to specific industrial needs.
Q2: How do CNC Milled parts differ from CNC Turned parts?
CNC Milled parts are crafted by moving cutting tools across stationary material, suitable for complex shapes. CNC Turned parts are formed by rotating the material against fixed tools, ideal for cylindrical parts.
Q3: Why choose CNCRUSH for your CNC machining service?
With over 12 years of experience, CNCRUSH provides expert CNC milling and turning services with advanced quality control, meeting the demanding standards of automotive, machine building, and automation clients.
Q4: What materials can be machined?
We specialize in aluminum, stainless steel, brass, and various plastics, adjusting machining parameters to ensure the best outcome for each material.
Q5: Can CNCRUSH handle both prototypes and large-scale production?
Yes, we serve small prototype runs as well as high-volume manufacturing, providing consistent quality across all production scales.
Conclusion
Mastering CNC machining techniques is vital for manufacturers aiming to deliver high-quality custom metal parts. The seven powerful techniques discussed — from high-speed milling to in-process inspection — collectively elevate the manufacturing process, ensuring precision, durability, and efficiency.
CNCRUSH leverages these advanced methods within a fully equipped factory to provide trusted cnc machining service focusing on both CNC Milled parts and CNC Turned parts for industries including automotive, machine building, and automation.
For companies seeking reliable partners to meet complex machining demands with passion and expertise, CNCRUSH offers a proven track record and cutting-edge capability. Visit our website to explore how we can help bring your custom metal part projects to life.