CNC machining for custom metal parts is revolutionizing manufacturing. Learn the best practices for CNC machining, focusing on CNC Milled parts and CNC Turned parts, and discover how our CNC machining service can enhance your automotive, machine building, and automation projects.
Introduction
CNC machining has transformed the landscape of metalworking. With the advent of Computer Numerical Control (CNC) machines, industries from automotive to machine building have been able to achieve unparalleled precision and efficiency. Today, CNC machining services are crucial in the production of custom metal parts, allowing for complex designs and tight tolerances that were once thought impossible. In this article, we’ll explore the best practices for CNC machining, focusing on CNC Milled parts and CNC Turned parts, and how these methods are applied to modern industries.
At CNCRUSH, with over 12 years of experience, we specialize in providing high-precision CNC machining services, including both CNC milling and turning solutions. Based in China, our skilled team is dedicated to delivering quality parts for a wide range of industries, including automotive, machine building, and automation.
Why CNC Machining is the Future of Custom Metal Parts
Before diving into the best practices, it’s essential to understand why CNC machining is vital for manufacturing custom metal parts. The ability to produce consistent, high-quality components in a timely manner is one of the primary reasons why CNC machining has become indispensable in modern manufacturing.
With CNC machines, designs are no longer limited by the capabilities of manual machines. CNC milling and turning offer flexibility, precision, and scalability that enable manufacturers to cater to the specific needs of industries such as automotive, machine building, and automation. Whether it’s complex geometries or high-volume runs, CNC machining provides solutions that align with these industries’ rigorous demands.
1. Importance of Design Considerations in CNC Machining for Custom Parts
In CNC machining, design plays a critical role in determining the feasibility, cost, and quality of the final part. Good design practices ensure that the part can be efficiently and effectively produced while minimizing errors and machining time.
Key Design Tips:
- Simplicity is Key: The more complex a design, the more time and effort are needed for machining, which increases costs. Whenever possible, keep the design simple.
- Avoid Sharp Edges: Sharp corners can be difficult to machine and are prone to weaknesses. Rounded edges are preferred for better durability and easier machining.
- Tolerance and Fit: Always account for the material’s properties when specifying tolerances. Tight tolerances require specialized equipment and extra effort.
2. Understanding CNC Milling and Turning for Metal Parts
CNC milling and turning are the two most common types of CNC machining used for producing custom metal parts. Understanding the differences between the two and when to use each is crucial for producing high-quality parts.
- CNC Milling: This process involves a rotating cutting tool to remove material from a workpiece, typically in a horizontal or vertical orientation. It’s perfect for creating flat surfaces, slots, holes, and complex 3D shapes.
- CNC Turning: In CNC turning, the part rotates while the cutting tool remains stationary. It’s commonly used for cylindrical parts like shafts, bushings, and bolts. CNC turned parts are known for their high precision and smooth finish.
At CNCRUSH, we provide both CNC milled parts and CNC turned parts with the utmost precision, utilizing advanced CNC machines for the automotive and machine building industries.
3. Material Selection for CNC Machined Parts
Choosing the right material for your CNC machined parts is essential for ensuring performance, durability, and cost-efficiency. Metals like aluminum, steel, and brass are commonly used for CNC machining due to their excellent machinability and strength.
- Aluminum: Lightweight, corrosion-resistant, and easy to machine, aluminum is often used in industries like automotive and aerospace.
- Steel: Known for its strength and durability, steel is commonly used for parts that need to withstand heavy loads or high temperatures.
- Brass: Brass is a versatile material with good machinability, commonly used for components that require high corrosion resistance and electrical conductivity.
4. How Tolerances Impact CNC Machining Process and Part Quality
The ability to produce parts with precise tolerances is one of the main advantages of CNC machining. However, maintaining tight tolerances often requires a careful balancing of design considerations, material properties, and machining capabilities.
- Why Tolerances Matter: Tight tolerances can ensure that the part fits perfectly in the assembly, reducing the need for post-machining adjustments.
- Cost vs. Precision: While tighter tolerances can improve part performance, they also increase machining time and cost. It’s important to assess the need for precision and balance it with the project’s budget.
5. CAD and CAM Integration for CNC Machining
The integration of Computer-Aided Design (CAD) and Computer-Aided Manufacturing (CAM) software is vital for efficient CNC machining. CAD software allows for the creation of detailed part designs, while CAM software generates the machining instructions.
- CAD Software: CAD allows engineers and designers to create 3D models of the part, including all specifications, dimensions, and material requirements.
- CAM Software: CAM software converts the CAD model into machine-readable instructions, guiding the CNC machine in the precise execution of the design.
Both CAD and CAM integration are essential to achieving high-quality CNC milled parts and CNC turned parts, and they streamline the manufacturing process.
6. Optimizing CNC Machining Efficiency and Reducing Costs
Efficiency is key to achieving affordable CNC machining services. By optimizing the design and machining process, manufacturers can reduce material waste, minimize machine downtime, and improve production speed.
Cost-Reduction Tips:
- Consolidate Parts: If possible, design parts that combine multiple components into a single piece to reduce assembly costs.
- Tool Path Optimization: Use efficient tool paths to minimize the time spent on machining operations.
- Choose the Right Materials: Selecting materials that are easier to machine can reduce costs and improve machining speed.
7. CNC Machining and the Automotive Industry
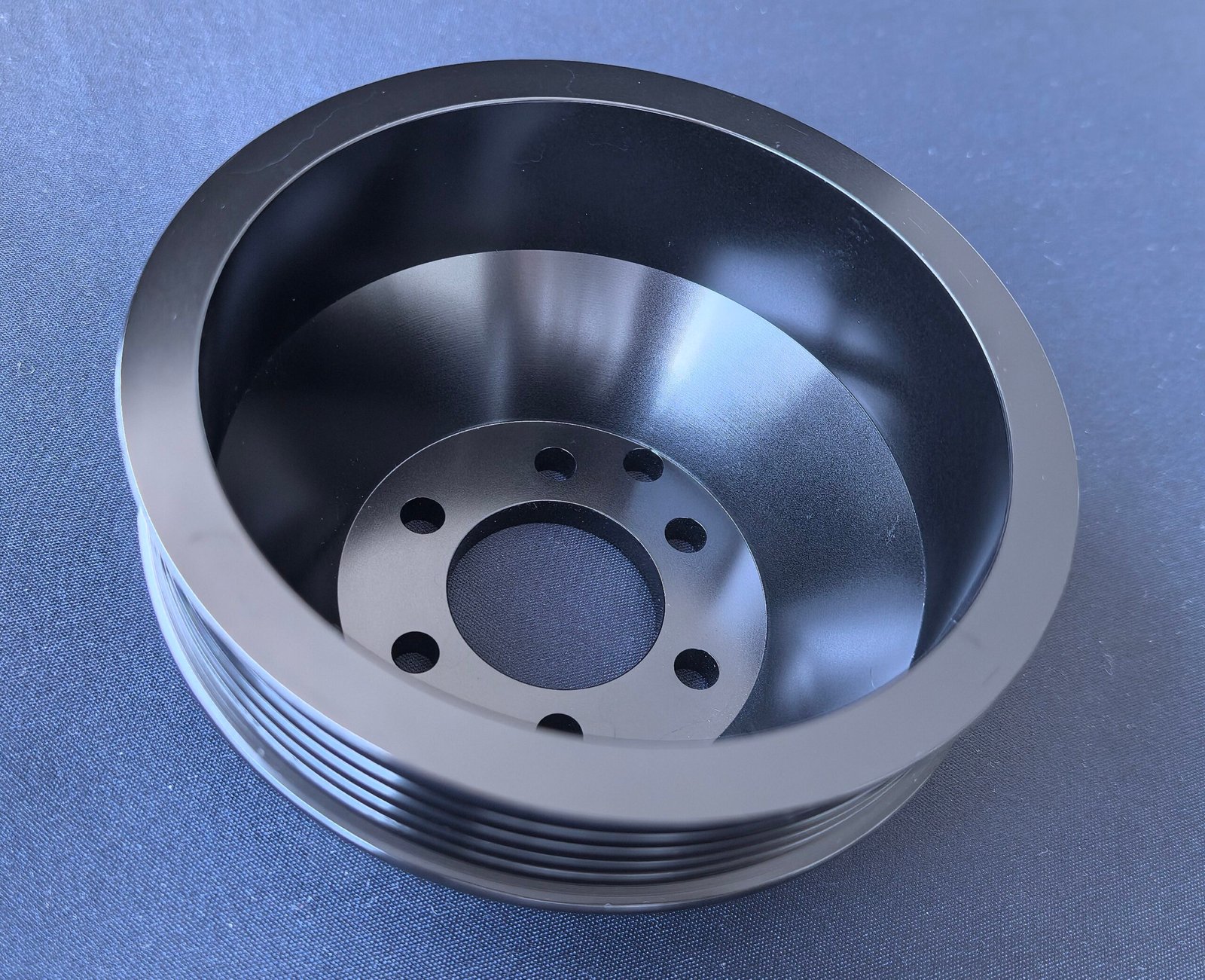
The automotive industry heavily relies on CNC machining for producing custom metal parts such as engine components, transmission parts, and braking systems. CNC milled and turned parts ensure high precision and durability, making them ideal for automotive applications.
- Quality and Safety: Automotive components require stringent quality standards to ensure safety and performance. CNC precision machining helps meet these standards by producing parts with precise dimensions and tolerances.
- Customization: CNC machining offers the flexibility to produce custom parts for various automotive models, providing manufacturers with the ability to cater to unique specifications.
8. CNC Machining for Machine Building and Automation
Machine building and automation require custom metal parts that are precise, reliable, and durable. CNC machining is crucial for producing components such as gears, shafts, and brackets for automated machinery and robotic systems.
- Precision Components: CNC machining provides the precision required for automated systems where even slight inaccuracies can lead to malfunctions.
- Efficiency and Speed: CNC machining allows manufacturers to produce parts quickly, enabling the efficient assembly of machines and systems.
9. The Role of CNC Machining in Prototyping and Product Development
Prototyping is a crucial stage in product development, and CNC machining plays a significant role in creating functional prototypes with high accuracy. This allows engineers to test the design and functionality of parts before committing to large-scale production.
- Speed to Market: CNC manufacturing enables fast prototyping, which helps businesses reduce time-to-market for new products.
- Iterative Design: With CNC manufacturing, designers can easily make adjustments to prototypes, improving the design iteratively based on testing feedback.
10. Why Choose CNCRUSH for Your CNC Machining Needs
With over 12 years of experience, CNCRUSH offers high-quality CNC manufacturing services tailored to your needs. Whether you require CNC milled parts or CNC turned parts, we specialize in delivering precision and custom solutions for industries such as automotive, machine building, and automation.
- Expertise: Our team has the knowledge and experience to handle complex designs and deliver the highest quality results.
- Global Reach: Based in China, we provide CNC machining services to clients around the world, offering competitive pricing without compromising quality.
FAQs
Q1: What materials can be used for CNC manufacturing?
A1: CNC manufacturing can handle a variety of materials, including aluminum, steel, brass, and plastics. The choice of material depends on the part’s requirements, such as strength, weight, and corrosion resistance.
Q2: How do I choose between CNC milling and CNC turning?
A2: CNC milling is ideal for creating flat, 3D shapes, while CNC turning is better for producing cylindrical parts. The choice depends on the geometry of the part you’re designing.
Conclusion
CNC machining is an essential technology for producing custom metal parts across various industries. By following the best practices outlined in this article, manufacturers can ensure high-quality parts, optimized production processes, and reduced costs. At CNCRUSH, we offer professional CNC machining services, including CNC milled parts and CNC turned parts, to help bring your designs to life with precision and efficiency.
For high-quality, affordable CNC machining services, visit CNCRUSH today!