The aerospace industry relies heavily on CNC milling and turning to produce high-precision components essential for the safety and performance of aircraft and spacecraft. The complexity of aerospace components, coupled with strict safety and quality standards, demands advanced machining techniques and expertise. This article explores the unique challenges in CNC machining for aerospace, offering insights into how CNC milling and turning are used to meet these demands and deliver high-quality components.
At CNCRUSH, we specialize in providing expert CNC Milling and turning services for the aerospace industry. With over 12 years of experience, we have the expertise and capabilities to produce CNC Milled parts and CNC Turned parts that meet the stringent requirements of aerospace manufacturers. Our services cater to industries such as automotive, machine building, and automation, offering precision and reliability in every project.
1. The Role of CNC Milling and Turning in Aerospace Manufacturing
CNC milling and turning are two critical processes used in the production of aerospace components. Milling involves using rotary cutters to remove material from a workpiece, while turning shapes parts by rotating the workpiece against a cutting tool. Both processes allow for the precise fabrication of complex geometries and high-tolerance parts that are essential in aerospace applications.
Aerospace components such as fuselage sections, engine parts, landing gear, and intricate avionics systems are often produced using these techniques. The precision required for aerospace parts means that even the slightest deviation in dimensions can result in part failure, which can have catastrophic consequences in-flight. As such, CNC machining is a vital technology for ensuring both precision and repeatability in aerospace manufacturing.
2. Challenges in CNC Milling and turning for Aerospace
CNC machining for the aerospace industry presents several unique challenges due to the nature of the parts being produced and the materials used. These challenges include:
- Complex Geometries: Aerospace components often have intricate shapes and tight tolerances.
- Exotic Materials: Titanium, Inconel, and other high-performance alloys are difficult to machine.
- Tight Tolerances: Aerospace parts must meet stringent dimensional and performance standards.
- Regulatory Compliance: CNC aerospace components must adhere to industry certifications like AS9100 and ISO 9001.
Overcoming these challenges requires advanced CNC technology, skilled operators, and a deep understanding of material properties and machining processes.
3. Overcoming Material Challenges in Aerospace CNC Milling and turning
The aerospace industry uses exotic materials such as titanium alloys, Inconel, and composites, which are chosen for their strength, lightweight properties, and resistance to extreme temperatures. However, these materials are often difficult to machine due to their hardness and tendency to generate heat during the cutting process.
Solutions:
- Use specialized cutting tools such as carbide-tipped or diamond-coated tools.
- Implement high-pressure coolant systems to dissipate heat and prevent material deformation.
- Optimize cutting speeds and feed rates to balance tool wear and machining efficiency.
Material | Properties | Challenges |
---|---|---|
Titanium | High strength-to-weight ratio | Prone to heat buildup and tool wear |
Inconel | Excellent heat resistance | Difficult to machine, requires slower speeds |
Aluminum Alloys | Lightweight and corrosion-resistant | Easier to machine but requires precision |
4. Addressing Component Size and Complexity
Aerospace components vary in size and complexity, from small, intricate parts to large structural sections. Machining large parts, such as fuselage sections or engine housings, presents a challenge due to the size constraints of machine tools and the need for precise material removal.
Solutions:
- Utilize 5-axis CNC machines that allow for complex geometries to be machined in fewer setups.
- Ensure rigid fixturing to prevent part movement during machining, especially for large components.
- Use software simulations to predict tool paths and avoid collisions.
5. Meeting Precision and Tolerance Requirements
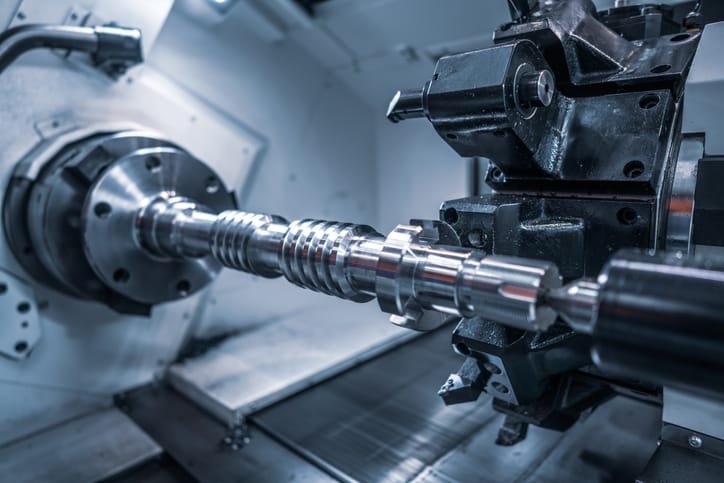
Precision is paramount in aerospace machining. Components must fit together perfectly to ensure the aircraft functions correctly and safely. Even a micron-level deviation can lead to performance issues or part failure.
Solutions:
- Implement advanced CNC programming techniques to control tool paths with high accuracy.
- Use precision measuring equipment such as CMM (Coordinate Measuring Machines) to inspect parts at every stage of production.
- Apply closed-loop control systems to monitor and adjust machining parameters in real-time, ensuring consistent accuracy.
6. CNC Milling for Aerospace Parts: Precision and Versatility
CNC milling is ideal for creating complex aerospace components, such as turbine blades, airframes, and control surfaces. 5-axis CNC milling machines can handle intricate geometries, enabling the production of parts with tight tolerances and complex surfaces.
At CNCRUSH, we specialize in producing CNC Milling and turning parts for the aerospace industry. Our 5-axis milling capabilities allow us to create precise, high-quality components that meet the stringent requirements of aerospace manufacturers.
7. CNC Turning for Aerospace Parts: Speed and Efficiency
CNC turning is used to produce cylindrical aerospace components such as shafts, engine components, and fasteners. This process is highly efficient and can produce parts with excellent surface finishes and dimensional accuracy.
CNCRUSH offers expert CNC Turned parts production for aerospace applications, ensuring fast turnaround times and high-quality results. Our advanced turning capabilities allow us to meet the tight deadlines and exacting standards of the aerospace industry.
8. Reducing Lead Times and Costs in Aerospace CNC Milling and turning
Lead times are critical in aerospace manufacturing, where delays can result in significant costs. CNC Milling and turning offers the ability to produce parts quickly and accurately, reducing the need for rework and speeding up the production process.
Solutions:
- Implement lean manufacturing principles to streamline production processes and eliminate waste.
- Use automated CNC systems to run lights-out machining operations, increasing production efficiency.
9. Ensuring Quality and Compliance with Aerospace Standards
Aerospace manufacturers must adhere to strict quality standards, including AS9100 and ISO 9001 certifications. Compliance with these standards ensures that parts are produced with the highest level of precision and safety.
Solutions:
- Implement robust quality control systems to inspect parts at every stage of production.
- Maintain full traceability of materials and processes to meet regulatory requirements.
10. The Future of CNC Milling and turning in Aerospace
As the aerospace industry continues to evolve, CNC Milling and turning will remain a key technology in the production of aircraft and spacecraft components. Advances in materials, machining techniques, and automation will drive further improvements in precision, efficiency, and cost-effectiveness.
At CNCRUSH, we are committed to staying at the forefront of CNC machining technology, providing our aerospace clients with the highest quality CNC Milled parts and CNC Turned parts. With over a decade of experience, we are your trusted partner for all your CNC machining needs.
FAQ
Q1. What materials are commonly used in aerospace CNC machining?
Titanium, Inconel, aluminum alloys, and engineering plastics such as PEEK and Ultem are commonly used due to their strength, lightweight properties, and resistance to extreme temperatures.
Q2. How does 5-axis CNC machining benefit aerospace manufacturing?
5-axis CNC machining allows for the creation of complex geometries with fewer setups, reducing machining time and increasing precision.
Q3. Why is precision so important in aerospace CNC machining?
Precision ensures that parts fit together correctly and function as intended, which is crucial for the safety and performance of aerospace components.
For expert CNC machining services that deliver precision and quality for aerospace applications, trust CNCRUSH. Contact us today to learn more about our CNC milling and turning solutions!