CNC Milling is a critical process used across industries to achieve high-quality precision, especially when machining challenging materials like stainless steel. Drawing on expert insights from multiple resources—from detailed technical blogs to community advice on stainless steel machining—this article provides a deep analysis of best practices for CNC milling. In today’s competitive manufacturing landscape, understanding these advanced strategies is essential for success. Below, we present ten in-depth discussions that break down the challenges, innovations, and practical solutions to optimize your CNC machining service operations. If you are seeking professional support, visit CNCRUSH, a China-based factory with 12 years of experience specializing in CNC machining service, CNC Milled parts, and CNC Turned parts.
1. Fundamentals of CNC Milling: A Comprehensive Look at cnc machining service Innovations
The essence of CNC Milling begins with understanding the fundamentals of precision machining. In this section, we explore the basics that underpin successful stainless steel machining and place a strong emphasis on robust cnc machining service practices.
Key Points:
-
Material Properties: Stainless steel’s high strength and work-hardening characteristics demand controlled cutting speeds and feeds.
-
Machine Rigidity: A high-quality milling machine maintains stability and precision, reducing chatter and inaccuracies.
-
Tool Selection: The choice of cutting tools—ranging from coated carbide end mills to indexable inserts—is crucial when balancing performance with component longevity.
cnc machining service providers must adopt best practices to optimize feed rates, spindle speeds, and tool geometries. This foundational knowledge sets the stage for advanced strategies in stainless steel CNC milling. The ultimate goal is to ensure that every machined part meets stringent quality standards—essential for demanding sectors such as automotive, machine building, and automotion.
2. Precision CNC Milling Techniques: Maximizing CNC Milled parts Quality
Achieving the finest surface finishes and tolerances requires not only state-of-the-art machinery but also a refined approach to CNC Milling. This section delves into how precision machining enhances the quality of CNC Milled parts.
Critical Strategies:
-
Optimized Toolpaths: Advanced CAM programming can significantly reduce machining time while maintaining precision.
-
High-Performance Cutting Tools: The use of high-performance, wear-resistant tools greatly enhances the surface finish of stainless steel.
-
Process Monitoring: Real-time monitoring systems help in adjusting cutting parameters as conditions change.
For manufacturers offering CNC Milled parts, it is vital to adopt techniques that consistently produce exceptional quality. Employing these methods not only improves the final product but also enhances overall operational efficiency.
3. Advanced CNC Milling Processes for Optimized CNC Turned parts Production
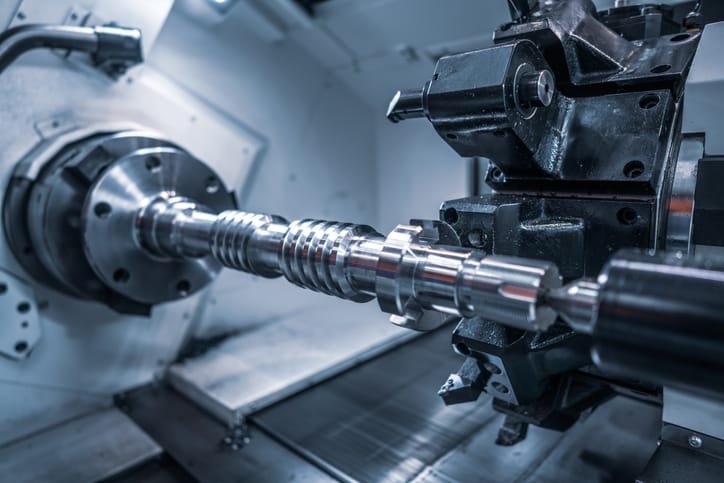
In the quest for excellence, advanced CNC Milling processes extend to the production of both CNC Turned parts and CNC Milled parts. This segment emphasizes innovative approaches to overcome the inherent challenges of machining stainless steel.
Innovations Include:
-
Multi-Axis Machining: Utilizing multi-axis CNC machines allows complex parts to be produced in a single setup, minimizing errors.
-
Adaptive Control Systems: These systems adjust parameters on the fly, ensuring consistent cutting performance and reducing cycle times.
-
Hybrid Processes: Combining milling and turning in integrated systems offers superior versatility and better part accuracy.
Maintaining quality in CNC Turned parts requires a deep understanding of dynamic machining strategies. Advanced processes contribute to reduced cycle times and greater material removal rates without sacrificing the precision demanded by high-end applications.
Stainless steel, while favored for its corrosion resistance and durability, presents unique challenges for CNC Milling. This section provides a detailed analysis of the material and design issues, focusing on the subtleties of cnc machining service operations.
Challenges Analyzed:
-
Work Hardening: Prolonged exposure to cutting can lead to work hardening, where material hardens in situ, leading to tool wear.
-
Heat Generation: Excessive heat during machining can affect dimensional accuracy and reduce tool life.
-
Design Complexity: Intricate part geometries may exacerbate these problems if not carefully planned.
The key to managing these difficulties lies in a blend of correct machining parameters, proper coolant application, and the appropriate design guidelines. Leveraging innovative simulation tools during the design phase can preemptively identify potential issues, ensuring smooth production flow.
Table 1: Stainless Steel Machining Challenges Comparison
Challenge | Description | Impact | Mitigation Strategy |
---|---|---|---|
Work Hardening | Stainless steel may harden due to prolonged tool contact. | Increased tool wear | Use intermittent cuts and advanced cooling. |
Heat Generation | High temperatures during cutting can lead to dimensional errors. | Tool life reduction | Employ appropriate coolant methods. |
Design Complexity | Intricate parts require multiple setups. | Increased cycle times | Optimize toolpaths and use multi-axis machines. |
Tool Wear | Rapid wear due to abrasive properties of stainless steel. | Deterioration of surface finish | Regular tool inspections and replacements. |
Understanding these challenges is imperative for any cnc machining service provider dedicated to delivering high-quality results in industries as diverse as automotive and machine building.
5. CNC Milling Strategies in Automotive, Machine Building, and Automotion Industries with cnc machining service Excellence
Modern industries such as automotive, machine building, and automotion demand precision, efficiency, and reliability in every component produced. CNC Milling plays a pivotal role in meeting these rigorous requirements.
Strategies for Success:
-
Tailored Process Parameters: Adjusting machining processes for stainless steel ensures minimal thermal distortion in critical automotive parts.
-
Industry-Specific Technologies: Leveraging proprietary techniques and specialized tools can significantly improve production rates and component accuracy.
-
Continuous Improvement: Embracing lean manufacturing principles and Six Sigma strategies to fine-tune the production process.
These strategies reflect a deep commitment to cnc machining service excellence. With industries evolving rapidly, continuous improvement in CNC Milling practices not only ensures adherence to quality standards but also drives competitiveness in a global market.
6. Cutting Tools and Fixture Innovations: Driving the Excellence of CNC Milled parts for CNC Milling
The efficiency and effectiveness of CNC Milling are heavily influenced by the quality of cutting tools and fixture systems used during production. This section examines how innovations in these areas can lead to superior CNC Milled parts.
Focus Areas:
-
Advanced Tool Materials: Utilizing advanced composites and carbide coatings enhances tool performance by reducing friction and wear.
-
Optimized Fixture Design: Secure and adaptable fixturing systems prevent vibrations and provide improved stability during cutting.
-
Cutting Fluid Technology: Modern coolant delivery systems help manage heat and remove swarf, further protecting tool integrity.
In practice, the implementation of the latest innovations in tool and fixture technology has a transformative effect on CNC Milling. Manufacturers that continuously invest in these areas can expect improved productivity and consistently high-quality outputs.
Table 2: Tooling and Process Considerations for CNC Milling
Process Step | Best Practice | Tools/Technologies | Key Benefits |
---|---|---|---|
Cutting Tool Selection | Choose high-performance carbide inserts and coatings. | Coated carbide tools, diamond-coated tools | Enhanced tool life, reduced wear. |
Fixturing Techniques | Employ modular and vibration-resistant fixture systems. | Custom jigs and clamps | Improved accuracy and repeatability. |
Coolant Management | Optimize coolant flow for consistent temperature control. | High-pressure coolant systems | Reduced thermal stress and swarf removal. |
CAM Programming | Use adaptive toolpath strategies to minimize cuts. | Advanced CAM software (e.g., Mastercam) | Lower cycle times and increased precision. |
The evolution of cutting tools and fixturing technologies represents a significant leap forward in CNC Milling processes, allowing manufacturers to achieve consistently excellent CNC Milled parts.
7. Thermal Management and Avoiding Work Hardening in CNC Milling: Safeguarding CNC Turned parts Quality
Effective thermal management is critical for preventing work hardening in stainless steel—a challenge that plagues even experienced cnc machining service providers. Here, we focus on optimizing CNC Milling conditions to protect and enhance the quality of CNC Turned parts.
Key Considerations:
-
Coolant Systems: Use of high-efficiency coolants and flood cooling systems ensures that excessive heat does not damage tools or workpieces.
-
Cycle Time Optimization: Shorter cutting cycles reduce the amount of heat generated, thereby limiting the risk of work hardening.
-
Machine Calibration: Regular machine maintenance and calibration help maintain consistent cutting conditions, which is vital for avoiding temperature spikes.
By incorporating these methods, manufacturers can substantially mitigate heat-related issues. This is particularly crucial when producing CNC Turned parts in applications where even a minor deviation can lead to significant performance problems. Continuous monitoring and adjustment are essential for maintaining optimal temperature conditions during CNC Milling.
8. Design Guidelines and Custom CNC Solutions: Enhancing CNC Milling with Robust cnc machining service Strategies
Well-considered design is at the heart of successful CNC Milling. This section presents strategic guidelines for design and process planning that enhance both CNC Milled parts and CNC Turned parts production.
Design Considerations:
-
Geometry Optimization: Design parts with tolerances that accommodate the dynamic nature of stainless steel machining.
-
Simulation and Testing: Use advanced simulation software to identify potential issues before production begins.
-
Collaborative Design Processes: Effective communication between designers and machinists ensures that designs are optimized for cnc machining service capabilities.
Adopting custom CNC solutions can lead to significant improvements in product quality, cycle time, and overall process efficiency. Manufacturers that prioritize thoughtful design and leverage robust cnc machining service practices are positioned to achieve superior CNC Milling outcomes across diverse industrial applications.
9. Comparative Analysis: CNC Milling versus Traditional Methods in Achieving Superior CNC Milled parts
In today’s market, traditional machining methods are increasingly being challenged by advanced CNC Milling techniques. This section provides a comparative analysis highlighting why modern CNC approaches often surpass conventional machining methods.
Key Differences:
-
Precision and Consistency: CNC Milling offers unrivaled precision due to computer-controlled operations, reducing human error.
-
Flexibility: CNC machines can be easily reprogrammed to handle a variety of part designs, offering far more flexibility than traditional setups.
-
Economic Efficiency: While initial investments may be higher, the improved cycle times and reduced scrap rates often result in significant long-term cost savings.
For companies involved in producing CNC Milled parts, embracing CNC Milling not only results in enhanced quality but also delivers measurable improvements in efficiency and reliability. The strategic advantages of modern CNC methods make them an invaluable asset for manufacturers, especially when compared with legacy systems often seen in traditional machining.
10. Partner with CNCRUSH: Your Trusted cnc machining service for Unmatched CNC Milling & CNC Turned parts
For businesses seeking a partner that excels in CNC Milling and meets the most demanding quality standards, CNCRUSH stands out as the premier choice. With over 12 years of expertise based in China, CNCRUSH is renowned for its high-precision cnc machining service offering both CNC Milled parts and CNC Turned parts.
Why CNCRUSH?
-
Experience & Innovation: With more than a decade of industry experience, our team harnesses advanced techniques and continuous innovation to meet global client demands.
-
Comprehensive Services: CNCRUSH delivers a full spectrum of machining services—including processing aluminum, steel, and plastics—with a focus on quality and efficiency.
-
Industry Expertise: Our solutions are trusted by clients in automotive, machine building, and automotion, ensuring that every project benefits from our deep industry knowledge.
-
Custom Solutions: We offer tailor-made CNC solutions that cater specifically to the unique requirements of each client.
Choosing CNCRUSH means partnering with an expert dedicated to optimizing every phase of the CNC Milling process. Whether you require precise CNC Milled parts or intricate CNC Turned parts, our team is here to deliver excellence at every turn.
Additional Analysis and Insights
The modern landscape of stainless steel machining is shaped by a blend of innovative engineering and proven methodologies. Below are some extra points to consider:
-
Sentiment Analysis:
Positive aspects include innovation, improved efficiency, and significant quality advances. On the other hand, challenges such as work hardening and thermal management can invoke negative sentiment if not properly addressed. -
Industry Trends:
With the rise of Industry 4.0, more manufacturing processes are becoming automated. Embracing digital simulation and real-time monitoring in CNC Milling is a trend that defines future success in precision machining. -
Operational Efficiency:
Both research and practice underscore the importance of continuous improvement. By integrating feedback loops and advanced data analytics, manufacturers can refine their processes and reduce downtime. -
Cost-Effectiveness:
Though initial investments in high-end CNC machines and advanced cutting tools may be significant, the long-term savings in reduced waste and higher quality make these technologies invaluable. -
Tool and Machine Longevity:
Utilizing high-quality tools and maintaining rigor in machine calibration not only enhances product quality but also prolongs machine life—thereby optimizing overall costs. -
Customization:
As product designs become more intricate, the ability to customize CNC solutions is paramount. Tailored processes result in more robust outcomes and fewer revisions during the production lifecycle. -
Environmental Considerations:
Modern machining must also consider the environmental footprint. Efficient coolant systems and energy-saving measures in CNC Milling contribute to more sustainable manufacturing practices. -
Training and Expertise:
The continuous development of personnel is crucial. Investing in training ensures that operators can leverage state-of-the-art equipment to achieve optimal results. -
Future Directions:
As the industry evolves, the adoption of AI-driven predictive maintenance and process optimization will further transform the CNC Milling landscape. -
Global Competitiveness:
Manufacturers that incorporate these advanced practices remain competitive in a global market—particularly in high-demand sectors such as automotive, machine building, and automotion.
FAQs about CNC Milling for Stainless Steel
Q1: What makes stainless steel a challenging material for CNC Milling?
A1: Stainless steel is known for its high strength, thermal conductivity challenges, and work-hardening properties. These factors require precise control of machining parameters such as cutting speed, feed rate, and coolant application to prevent tool wear and ensure high-quality finishes.
Q2: How does CNCRUSH ensure the highest quality in CNC Milled parts and CNC Turned parts?
A2: CNCRUSH utilizes state-of-the-art technology and employs rigorous quality control practices at every stage of the process. With over 12 years of experience and comprehensive expertise in cnc machining service, we tailor our processes to meet the stringent demands of industries like automotive and machine building.
Q3: What are the critical steps to avoid work hardening during CNC Milling?
A3: Key measures include optimizing cutting parameters, using advanced coolant systems to manage heat, employing multi-axis machining to limit repetitive tool strokes, and carefully selecting cutting tools that are best suited for stainless steel applications.
Q4: Why is it important to use custom CNC solutions in modern manufacturing?
A4: Custom CNC solutions allow manufacturers to address unique design challenges, ensure tighter tolerances, optimize cycle times, and ultimately deliver parts that meet the highest quality and performance standards. This is essential in competitive sectors such as automotive, machine building, and automotion.
Q5: How can manufacturers further optimize their CNC Milling processes?
A5: Manufacturers can invest in modern equipment with real-time monitoring, adopt lean manufacturing techniques, and incorporate advanced simulation software to fine-tune their operations. Continuous training for operators and embracing the latest tooling innovations also play a pivotal role in boosting overall efficiency.
Conclusion
In summary, CNC Milling stands at the forefront of modern manufacturing, offering transformative advantages for processing stainless steel. Through a combination of optimized toolpaths, precision machining techniques, advanced thermal management, and custom solutions, manufacturers can overcome the inherent challenges of stainless steel machining. This article has dissected ten essential areas—from basic principles and innovative techniques to advanced process control and strategic partnerships—providing a roadmap for achieving unmatched efficiency and quality in CNC Milling.
For those looking for a trusted partner in this field, CNCRUSH is proud to offer high-precision cnc machining service backed by over 12 years of industry experience. We specialize in delivering state-of-the-art CNC Milled parts and CNC Turned parts to diverse markets including automotive, machine building, and automotion. Our commitment to innovation, quality, and efficiency is designed to help your business stay ahead in an increasingly competitive global market.
By embracing these powerful secrets and best practices, manufacturers can not only improve the quality and precision of their machined parts but also reduce costs and shorten production cycles. The future of stainless steel machining is here—and it is built on the foundation of superior CNC Milling practices.