High-precision CNC turning solutions are essential for the medical industry. Discover 10 key benefits of CNC turning for medical devices and how our CNC machining services can elevate your manufacturing process.
Introduction
CNC turning has become a cornerstone of high-precision manufacturing, particularly in industries such as medical device production. The medical sector demands impeccable quality, precise measurements, and durable materials—requirements that CNC turning solutions are well-equipped to meet. At CNCRUSH, we specialize in providing precision CNC machining services, particularly CNC Milled parts and CNC Turned parts, for medical device manufacturers.
In this article, we will explore the role of CNC turning in the medical device industry, highlighting its advantages and applications, and demonstrating how CNCRUSH has helped medical device manufacturers streamline their production processes with high-quality, custom solutions. Let’s dive into the world of high-precision CNC turning and its invaluable contribution to healthcare advancements.
1. What is CNC Turning and How Does it Work?
CNC turning is a subtractive manufacturing process that involves rotating a part (usually cylindrical) on a machine called a lathe while a cutting tool removes material to achieve the desired shape. This precision process is controlled by a computer numerical control (CNC) system, which ensures consistency and accuracy throughout the manufacturing process. CNC turning can create intricate parts with precise tolerances, making it ideal for manufacturing medical components.
CNC turning is often used for creating parts that require high symmetry and exact dimensions, such as medical implants, surgical tools, and diagnostic equipment. The machine tools used in CNC turning allow for fast production cycles, complex geometries, and multi-axis cutting capabilities, all while maintaining precision and repeatability—key factors for medical device manufacturing.
2. The Importance of Precision in Medical Device Manufacturing
Precision is at the core of medical device manufacturing. Even slight deviations in dimensions can lead to catastrophic outcomes, especially when it comes to implants and surgical tools that directly interact with patients. This is where CNC turning excels—offering unparalleled accuracy that is crucial for ensuring patient safety.
Medical devices must meet strict regulatory standards and be manufactured to incredibly tight tolerances. For example, the International Organization for Standardization (ISO) 13485 standard ensures that medical devices are consistently produced and controlled according to quality management standards. CNC Milled parts and CNC Turned parts meet these requirements through rigorous process controls, making CNC turning an indispensable technique in the medical industry.
By using CNC turning, manufacturers can meet these stringent standards, resulting in products that are safer, more reliable, and of higher quality. This, in turn, fosters trust between manufacturers, healthcare providers, and patients.
3. Materials Used in CNC Turning for Medical Devices
In medical device manufacturing, the selection of materials is just as important as the machining process itself. CNC turning is highly versatile and can accommodate a wide variety of materials that meet the demanding needs of the medical industry.
Stainless steel, titanium, and medical-grade plastics are among the most common materials used in CNC turning for medical devices. These materials offer excellent biocompatibility—ensuring that devices do not cause adverse reactions when in contact with human tissue. For example, titanium is often used for orthopedic implants because of its strength, lightness, and corrosion resistance. Similarly, stainless steel is used for surgical instruments because it resists corrosion and can withstand high levels of sterilization.
CNC turning also accommodates other specialty materials, including PEEK (Polyetheretherketone), a high-performance polymer often used in medical applications like surgical implants and biomaterials. This wide material versatility enables CNC precision turning to be used across a wide range of medical device applications, ensuring reliability, safety, and long-term performance.
4. Key Advantages of CNC Turning in Medical Device Manufacturing
CNC turning offers several key benefits that make it the ideal choice for manufacturing medical device components:
1. High Precision and Repeatability
CNC turning ensures that each part produced is identical, maintaining exact dimensions and tolerances every time. This repeatability is critical for medical device manufacturers who must adhere to strict regulatory standards.
2. Flexibility in Materials
CNC turning is highly adaptable, able to work with a range of metals, plastics, and composite materials. This makes it the ideal choice for manufacturers who require diverse material options for various medical devices.
3. Efficient Production and Cost-Effectiveness
While CNC turning involves initial setup costs, it is highly cost-effective in the long run, particularly for small to medium batch production. The efficiency of CNC machines minimizes manual labor, reduces waste, and shortens production times.
4. Scalability
Whether a company is producing custom one-off medical parts or large production runs, CNC turning offers scalability that accommodates both. Manufacturers can easily scale from prototypes to full production without sacrificing quality or consistency.
5. CNC Turning vs. Traditional Machining Methods in Medical Device Production
Traditional machining methods, such as manual turning and milling, are often slower, more labor-intensive, and prone to human error. In contrast, CNC turning automates the entire process, ensuring higher precision, speed, and repeatability.
Advantages of CNC Turning Over Traditional Methods:
- Speed: CNC machines operate faster than manual machines, increasing throughput.
- Precision: CNC turning guarantees tighter tolerances and minimizes human error.
- Automation: CNC turning eliminates the need for manual adjustments, leading to fewer mistakes and more consistent results.
For medical devices, where consistency and accuracy are paramount, CNC turning is the superior option.
6. Applications of CNC Turned Parts in the Medical Industry
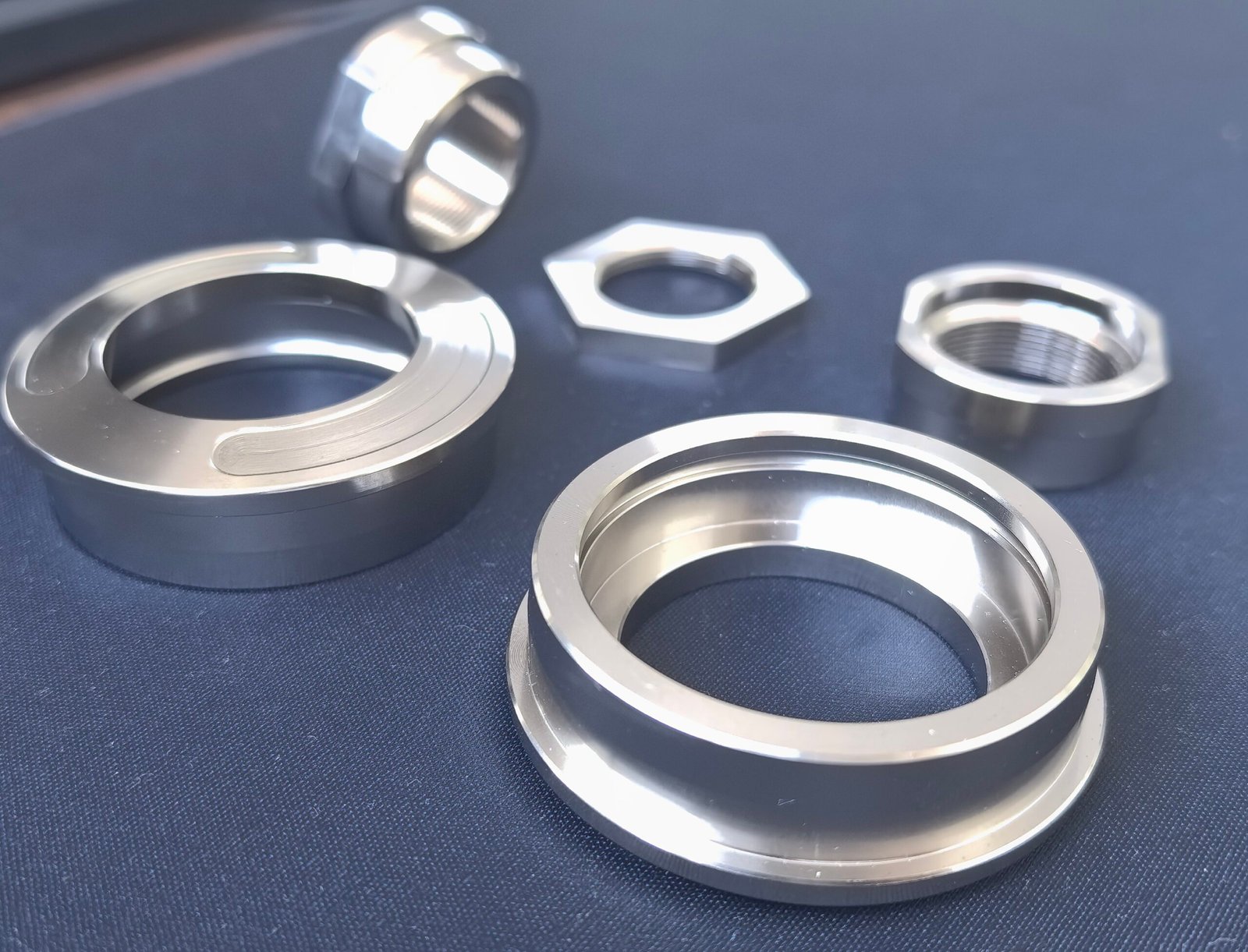
The versatility of CNC precision turning allows it to be used in a variety of medical device applications. Some common uses for CNC Turned parts in the medical industry include:
Surgical Tools:
Tools such as forceps, scissors, and scalpels require high-precision machining to ensure they perform safely and reliably during surgeries.
Orthopedic Implants:
Screws, plates, and joint replacements are commonly made using CNC turning. These parts need to meet strict requirements for strength, biocompatibility, and precision.
Diagnostic Equipment:
Parts used in diagnostic machinery, such as handles, connectors, and knobs, are often manufactured using CNC precision turning. These components must be durable and precise to ensure that diagnostic tools function effectively.
Dental Devices:
Implants, crowns, and bridges made using CNC precision turning must be highly detailed and biocompatible, offering both functional and aesthetic benefits for patients.
7. The Role of CNC Machining in Medical Device Regulatory Compliance
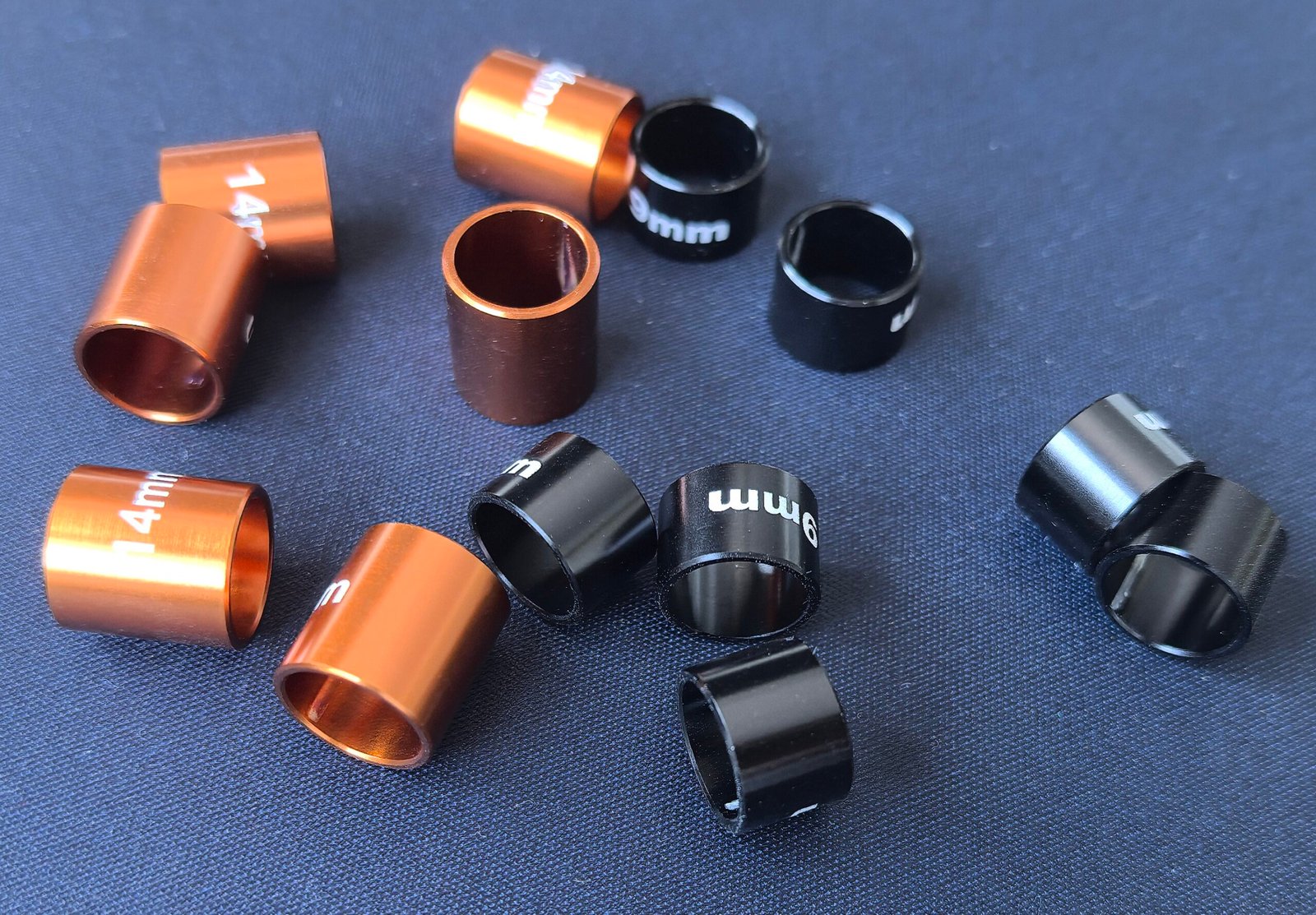
The medical device industry is highly regulated, and manufacturers must comply with strict guidelines to ensure patient safety. CNC machining plays a vital role in meeting these requirements, particularly in producing high-precision parts that adhere to ISO and FDA standards.
ISO 13485 is a key standard for medical devices, ensuring that manufacturers consistently produce quality parts. CNC precision turning helps ensure compliance with these regulations by providing traceability and high-quality machining, crucial for medical device certification.
At CNCRUSH, we are familiar with the importance of maintaining compliance, and we employ rigorous quality control measures to ensure that all our CNC Milled parts and CNC Turned parts meet these global standards.
8. Advantages of Partnering with a Specialized CNC Machining Service
Choosing a specialized CNC machining service like CNCRUSH offers numerous benefits for medical device manufacturers, including:
Expertise in CNC Turning and Milling:
With over 12 years of experience, CNCRUSH has honed its skills in high-precision CNC machining services, specializing in CNC Turned parts for the medical industry.
Quality Assurance:
We understand the critical nature of medical device manufacturing, which is why we adhere to strict quality control standards to ensure the highest possible precision and quality.
Custom Solutions:
We offer custom CNC solutions tailored to the unique needs of your project, whether it’s a one-off prototype or a large batch production run.
9. CNC Turning Solutions for the Future of Medical Devices
The future of medical devices is evolving rapidly, with new technologies like robotic surgery and 3D-printed implants becoming increasingly popular. CNC precision turning will continue to play a critical role in the manufacturing of these advanced medical devices.
As medical technology evolves, so do the needs for CNC machining. CNCRUSH is committed to staying at the forefront of these changes by investing in advanced CNC turning equipment and smart automation that enhances production speed and precision.
10. Why Choose CNCRUSH for Your CNC Turning Needs?
With over a decade of experience in CNC machining, CNCRUSH is a trusted partner for medical device manufacturers seeking high-precision CNC Turned parts. We specialize in offering CNC machining services that are efficient, cost-effective, and reliable.
Our Advantages Include:
- 12 years of experience in the CNC machining industry.
- Expertise in providing CNC Milled parts and CNC Turned parts for medical applications.
- A commitment to quality control and regulatory compliance.
- Competitive pricing for CNC machining in China without compromising quality.
For medical device manufacturers seeking precision, reliability, and cost-effectiveness, CNCRUSH is the ideal partner for your CNC precision turning needs.
Tables & Analysis
Table 1: Comparison of CNC Turning vs. Traditional Machining Methods
Factor | CNC Turning | Traditional Machining |
---|---|---|
Precision | High precision, tight tolerances | Lower precision, risk of errors |
Speed | Faster production cycles | Slower and less efficient |
Cost | Cost-effective for small batches | Higher labor and material costs |
Flexibility | Versatile in handling different materials | Limited to specific processes |
Automation | Fully automated | Requires manual labor |
Table 2: Materials Commonly Used in CNC Turning for Medical Devices
Material | Application | Benefits |
---|---|---|
Stainless Steel | Surgical tools, implants | Corrosion resistance, durability |
Titanium | Bone implants, prosthetics | Strength, lightness, biocompatibility |
PEEK | Surgical implants, biomaterials | Biocompatibility, strength, sterilization |
Medical-grade Plastics | Diagnostic equipment, dental devices | Lightweight, cost-effective, biocompatible |
Conclusion
CNC turning is indispensable in the manufacturing of high-precision medical device components. By choosing CNCRUSH as your partner, you can ensure that your devices meet the highest standards of quality, safety, and performance. From surgical tools to orthopedic implants, CNC turning provides a reliable and cost-effective solution for the future of medical technology.
Feel free to contact us at info@cncrush.com for more information or to request a quote for your next medical device project.